Oxímoron: Moggaro, un astillero en Segovia
En apenas doce años se han convertido en el primer astillero español de su clase y han tenido la mayor producción de barcos. Los hermanos Parga se lanzaron a fabricar “prácticamente sin experiencia”. En 2004, Santiago trabajaba en las obras del AVE: “Mi hermano y yo decidimos sustituir nuestro barco de fibra de vidrio, que ya estaba en mal estado, por otro de recreo de 5 metros para ir a pescar. José diseñó el barco y lo realizamos en una calderería local en Avilés, Asturias. Así fabricamos nuestro primer barco de aluminio”.
La reacción de los buceadores que acompañaron a los hermanos en la primera prueba de navegación fue determinante: “Fue tal el comportamiento del casco de aluminio respecto al de fibra, que todos quedamos prendados”, explica Santiago.
EXECUTIVE EXCELLENCE: ¿Cómo pasaron de la construcción artesanal de un barco en Asturias a crear un astillero en Segovia?
SANTIAGO PARGA: Coincidiendo con el proceso de fabricación de nuestro barco, conocimos a una empresa que se dedicaba a la construcción de cisternas de aluminio en Segovia, y aceptaron nuestro reto. Les trajimos el barco para que lo copiasen, mi hermano y yo hicimos personalmente todos los remates, y nos fuimos a una feria a Madrid. ¡Quienes vieron allí el barco se quedaron sorprendidos por la mala calidad de los acabados! Además, solo habíamos pintado la mitad para que se percibiera bien el aluminio.
Las personas que buscaban un barco de recreo lo miraban con recelo; sin embargo, los visitantes que se dedicaban al buceo sí apreciaban la resistencia y la dureza de los cascos de aluminio, pues era ideal para sus actividades profesionales y para resistir los choques de sus pesadas bombonas mucho mejor que los suelos de fibra de vidrio. Nos pidieron que construyéramos barcos de unos 8 metros de eslora, con capacidad para 12 buceadores. Ese fue nuestro inicio.
En aquel momento no podíamos competir con las embarcaciones de recreo de fibra de vidrio, pero a finales de 2004 estábamos en la Feria Náutica de Barcelona después de haber construido tres barcos de 5 metros y uno de 8. Estábamos al límite de nuestra capacidad financiera, éramos conscientes de que si no conseguíamos vender un barco allí, nuestros sueños se iban a pique, pero tuvimos suerte. Así logramos entrar en el sector de barcos para el buceo.
F.F.S.: Desde entonces han desarrollado varios proyectos. ¿De cuáles se siente más orgulloso?
S.P.: Uno de ellos es el proyecto de interceptoras. En el año 2013 recibimos un encargo de dos lanchas rápidas por una empresa española, destinadas a labores de intercepción, sin armamento, en el Caribe. Este proyecto tenía un requerimiento de 48,5 nudos de velocidad, y había que superar los 43 nudos que habíamos conseguido con una primera unidad hecha en otro astillero y que había resultado un fracaso.
Los clientes se habían sentido atraídos por nuestros barcos de pasajeros, que tienen una velocidad de 42 nudos, y se nos habían aproximado en un momento donde teníamos en construcción cinco jet boats y dos auxiliares de atunero (era el boom de la fabricación de atuneros, nos encargaron 20 auxiliares), con lo cual vieron “movimiento” y les generamos confianza.
Para el proyecto se tenía en cuenta una motorización de 2x400cv Volvo, cuyas especificaciones rondaban los 48 nudos de velocidad máxima. Hicimos un proyecto de casco más corto, reduciendo la manga (ancho) en 10 cm., pero con unas extensiones en proa que exteriormente le daban la misma dimensión. Quienes nos encargaron el proyecto se estaban jugando su credibilidad. Nosotros aceptamos ser penalizados si no alcanzábamos la velocidad solicitada. Decidimos construir el casco, comprar los motores y, sin terminar el barco, realizar una simulación de pesos con 2.500 kilos en sacos de arena. La colocación del centro de gravedad es el aspecto crítico de la construcción a la hora de obtener la velocidad requerida.
Nos fuimos a probarlo a Ribadeo. Nuestra idea original era probar primero el barco en vacío, pero la grúa descargó directamente el barco y no pudimos hacer más que la prueba de carga máxima. No debemos olvidar que Volvo nos decía que la velocidad máxima era de 48.5 nudos en vacío. Nosotros nos comprometimos a 45.8 nudos a plena carga. ¡En la primera vuelta alcanzamos 46.3!
Invitamos a los clientes que estaban allí a que se dieran una vuelta. Se sentaron, estando en plena carrera, en la zona de popa. Con los motores a todo gas, conseguimos 49 nudos fuertes atrás. Es decir, estábamos dando a máxima carga lo que nos pedían en vacío. Los clientes estaban emocionados, y recibimos el encargo de terminar el barco.
En las pruebas finales, además de los propietarios, nos acompañó Bureau Veritas para certificar la velocidad. ¡Logramos 45.8 nudos en mar abierto, con oleaje ondulado! Reconozco que la sensación es terrorífica. Además, quisieron simular una situación real haciendo todo tipo de giros. El momento fue tenso, pero creo que nunca he estado más orgulloso de una construcción.
Uno de los grandes atractivos de este diseño es que es muy polivalente y puede transformarse en un barco de recreo de alta velocidad, con un nivel de motorización y de consumo sensiblemente inferior a lo que hay ahora en el mercado, y por supuesto con un nivel de resistencia y fortaleza capaz de afrontar casi cualquier tipo de mar.
Otro motivo de orgullo es el proyecto de catamaranes para trabajos hidrográficos de la Marina de Venezuela, que consta de dos buques hechos a la medida, con un sistema de sonda por popa y proa.
Las pruebas del primer prototipo, realizadas en Ribadeo, han dado excelentes resultados. A través de Internet, una empresa española nos contactó en 2014 y se ofreció como nuestro representante en Venezuela. Partimos de unos modelos norteamericanos –más pequeñas y caros– para desarrollar las alternativas que fueron aceptadas, y que salieron adelante sin ni siquiera haberlos visto.
Este proyecto nos enseñó a gestionar los plazos. En los entornos públicos, los procesos son más complejos y lentos. Cuando finalmente se decidieron a construir ambos catamaranes, nos obligaron a unos tiempos de producción que presionaron mucho nuestra estructura. Tuvimos que subcontratar parte del trabajo –ya que en esos momentos teníamos 18 pedidos–, pero fue una buena experiencia de aprendizaje. Técnicamente, este proyecto ha sido un reto. El pasado 15 julio, el cliente estuvo navegando con ellos y desarrolló una lista de 40 requisitos añadidos, y bastantes cambios. El nivel de detalle exigido ha sido tremendo, pero los resultados les han dejado muy contentos.
E.E.: ¿Alguna otra embarcación preferente?
S.P.: Los jet boats. Conceptualmente, es como una moto de agua pero con 12 plazas. Un barco que alcanza 38 nudos, “derrapa” y hace trompos. Está propulsado por una turbina que puede invertirse yendo a toda velocidad, por lo cual el barco se sumerge. Es algo espectacular. Este estilo de embarcaciones –originaría de Nueva Zelanda– permite navegar en aguas muy poco profundas; tiene una turbina en vez de hélices, lo que le permite superar incluso los bancos de arena.
Vendimos el primer modelo en 2008. Al año siguiente, aun teniendo muchísima demanda, no había financiación. En 2010 vendimos tres, entre 2012 y 2013 vendimos más de una docena –algunos directamente construidos en México–. ¡En 2015 vendimos 19!
Todo el proceso de desarrollo ha sido tremendamente exigente. Las turbinas no fueron diseñadas para realizar decenas de paradas de emergencia al día y los barcos han tenido que ir mejorando la estanqueidad. Incluso ha habido que rediseñar los cuadros y los mandos, porque se sumergen bajo el agua continuamente. En permanente evolución, el barco no hace más que mejorar. Procuramos mantener un estrecho contacto con nuestros clientes, de manera que nos aporten más conocimiento para perfeccionar el producto.
Se está utilizando mucho en el Caribe, como un barco de entretenimiento turístico. Es una embarcación muy rentable, por ser una de las atracciones más demandadas. La gente se entusiasma cuando se sumerge. Para poder entenderlo bien, le sugiero visitar nuestra web: www.moggaro.com, o directamente en www.jetboateurope.com.
Lo que puede parecer algo “arriesgado”, no lo es. Acumulamos ya más de 17.000 horas de navegación que equivalen a 130.000 trompos y 130.000 frenadas sin una sola incidencia. Comparado con la célebre banana (un cilindro hinchado de grandes proporciones donde se sientan los pasajeros) es muchísimo más seguro, aunque no voy a negar que tenemos que luchar contra las “restricciones” que algunas capitanías marítimas plantean, más por desconocimiento que por cualquier hecho objetivo.
E.E.: ¿Qué porcentaje de la producción se destina a usos profesionales y a usos recreativos?
S.P.: Prácticamente el 50% de nuestra producción esta orientada a la fabricación de barcos turísticos del modelo del que estamos hablando. Este modelo ha mantenido vivo al astillero desde el año 2012 al 2015. También se incluye, en esta categoría, a los barcos dedicados al buceo.
E.E.: Un proyecto como este, alimentado esencialmente de la pasión, ¿cómo se mantiene a flote?
S.P.: Uno de los primeros problemas con el que nos encontramos al principio era que “desconocíamos” el precio de las cosas que fabricábamos. Los primeros años nos dedicamos esencialmente a invertir, investigar e innovar. Ahora soy consciente de que estuvimos vendiendo a coste, o por debajo de coste. Yo era el único en la empresa, el resto estaba subcontratado; apenas teníamos maquinaría... Pero fue el precio que que tuvimos que pagar para poder entrar en este mercado.
En los peores momentos de la crisis reciente, y tras haber vendido más de 70 embarcaciones, pensaba que con solo haber cobrado 2.000 euros más por cada barco –una nimiedad en relación al precio de venta de 70.000 euros–, nos habría sido de gran utilidad. El cliente siempre intenta negociar el precio final y la comparativa con los cascos de fibra es muy perjudicial. Solo los entendidos saben apreciar la diferencia. La gran ventaja es que las embarcaciones siguen ahí, soportando el paso del tiempo con mucha más soltura que cualquier otro tipo de embarcación. Por eso no es nada infrecuente que nuestros clientes repitan.
En barcos de pasaje, acabamos de hacer uno de 15 metros para 50 pasajeros por encargo de una empresa clásica del sector de Baleares, que tiene más 30 años de historia. Para ellos ha sido una decisión difícil comprarse un barco en Segovia. Sus dos propietarios, de más de 70 años, probaron primero un barco que tenemos en Barcelona, y con cierto escepticismo vinieron aquí. Su mercado es muy especial, pues están focalizándose en barcos rápidos para 50 personas.
En el mes de noviembre, estuvieron viendo el casco. La sensación de robustez que desprende un casco de aluminio les convenció. Además, teníamos también en construcción dos patrulleras, dos jet boats y un atunero. Recuerdo oírles decir: “Si vuelvo a Mallorca y cuento que acabo de estar en un astillero en Segovia, donde tienen seis barcos en construcción, no me cree nadie”.
Tras dos meses de tener su barco navegando, nos acaban de encargar otro de 18 metros de eslora, lo cual mantendrá ocupado a un equipo de cuatro personas durante siete meses. Estamos entrando en una fase muy positiva de clientes recurrentes.
Una parte esencial de nuestros servicios es la capacidad de adaptación. Hacemos las cosas a medida y hemos aprendido a ser capaces de aportar esos pequeños detalles que hacen felices a nuestros clientes.
E.E.: ¿Cuáles son las expectativas? ¿Qué tenéis en cartera?
S.P.: La suerte de tener mucho trabajo es que no te deja tampoco planificar a muy largo plazo. Imagino que nuestra relación con la empresa segoviana de Calderería, que les ha permitido subsistir en tiempos de crisis, tomará otros derroteros. Tenemos invitaciones para trabajar en entornos tan dispares como Corea.
Tecnológicamente, estamos analizando nuevos proyectos innovadores y abriendo instalaciones en el Cantábrico, ya que necesitamos lugares para realizar pruebas, y los costes de transporte son elevados.
Estos últimos años han pasado a una velocidad de vértigo. Si bien estuvimos a punto de desaparecer nada más nacer, creo que ya hemos superado esa etapa de infancia como empresa y estamos entrando en una fase de madurez.
El aluminio como material de construcción para los barcos aporta seguridad, eficiencia y resistencia. No es por casualidad que se utilice cada vez más en todo tipo de industrias. Estoy convencido de que tenemos por delante un futuro muy interesante y, personalmente, disfruto lo que hago con gran intensidad.
Entrevista publicada en Executive Excellence nº127 febrero 2016
Últimos artículos
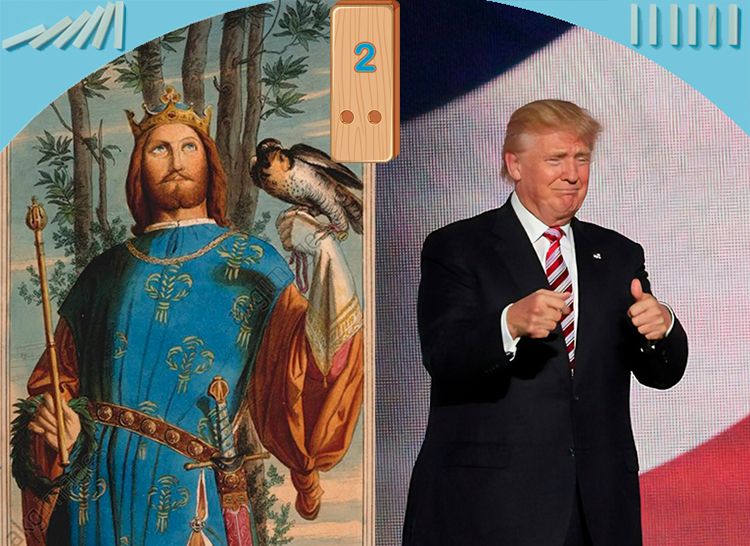
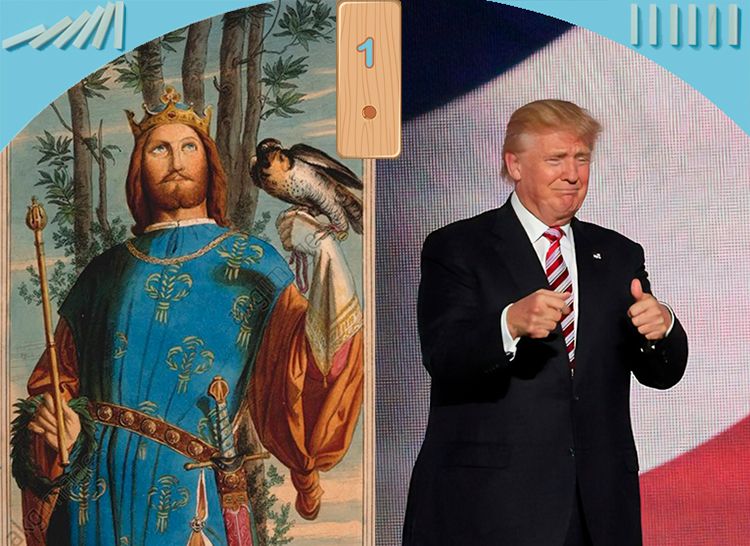
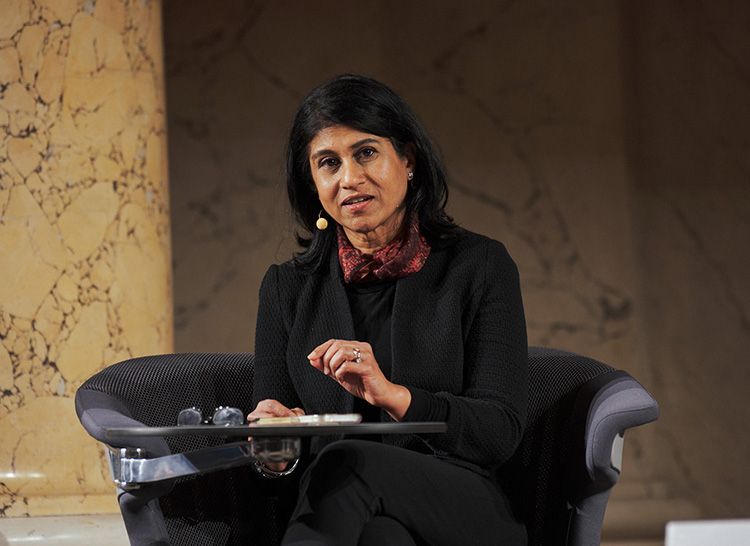
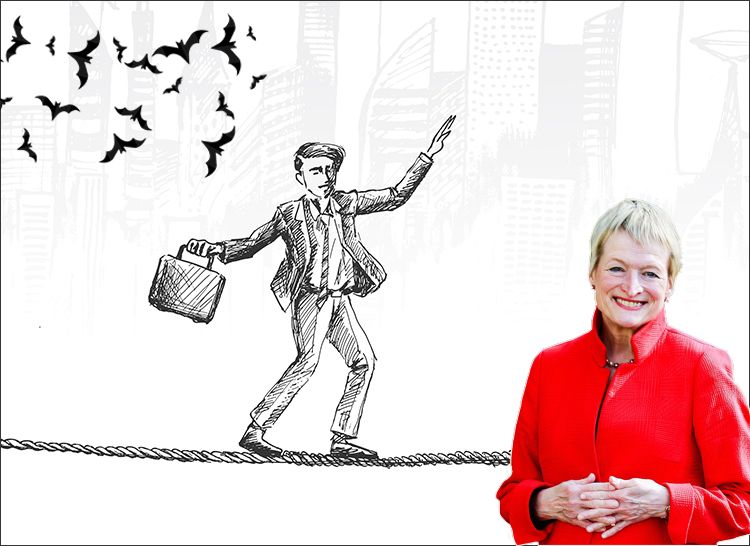
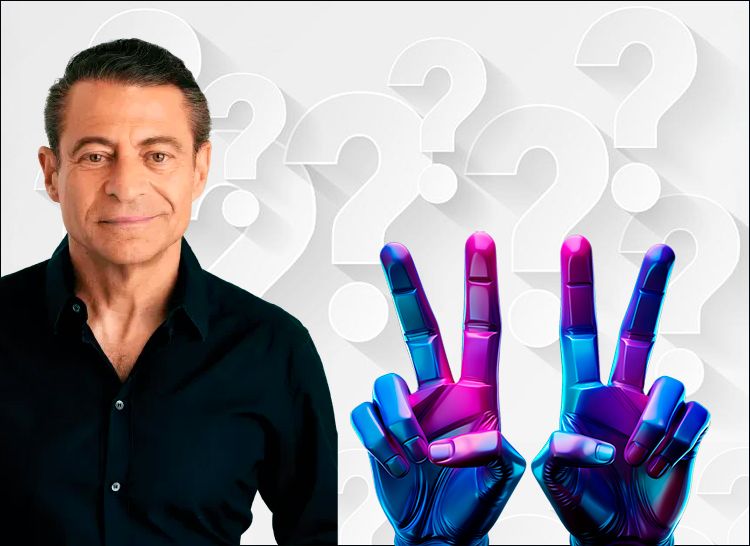
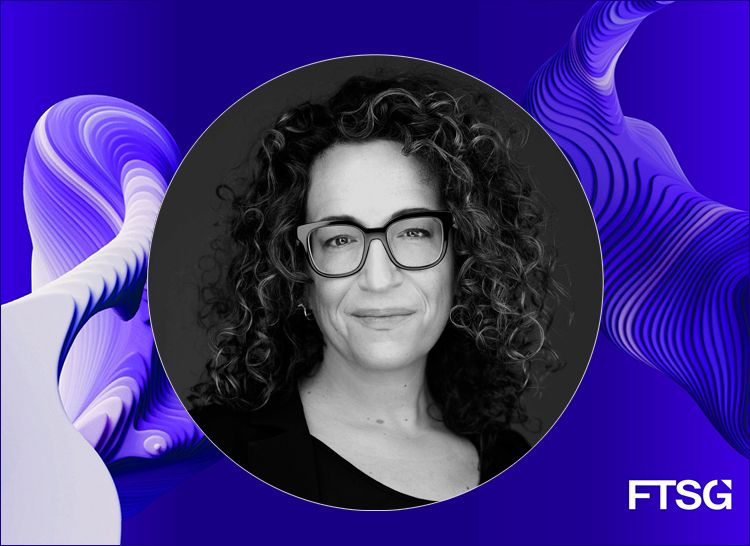